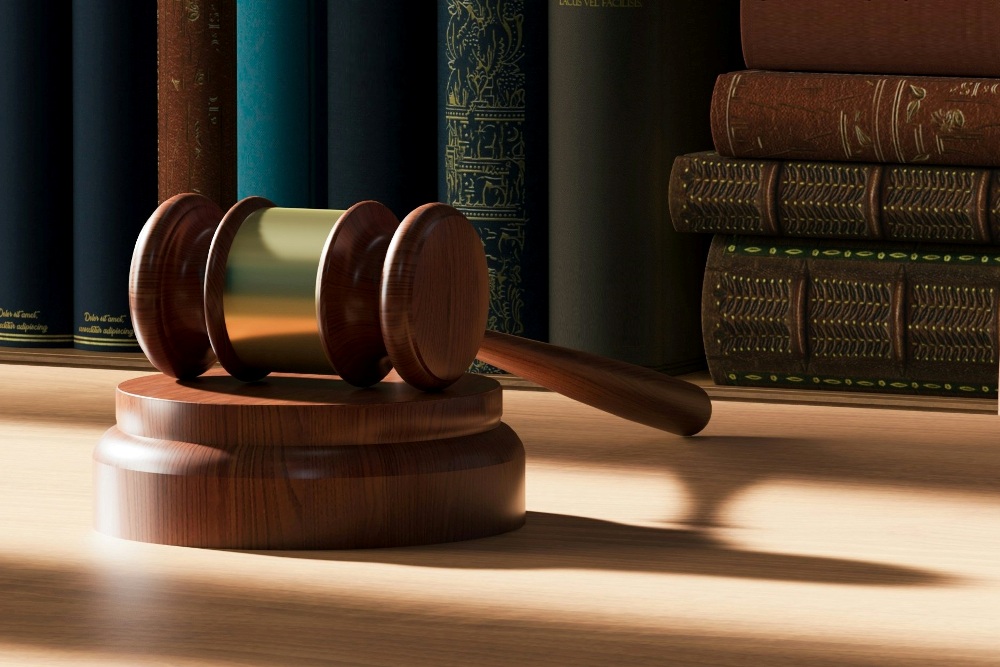
Workplace injuries often result from preventable hazards that go unnoticed until they cause harm. Creating a culture of safety begins long before any accident occurs by implementing proactive measures that protect employees and businesses alike. It requires a blend of clear safety protocols, thorough employee education, and vigilant maintenance routines that spot risks before they escalate. Every industry, whether manufacturing, office-based, or service-oriented, benefits when prevention takes priority over reaction. Investing effort into these steps transforms the workplace into a space where well-being is safeguarded, productivity thrives, and costly downtime diminishes. Approaching safety as an ongoing commitment instead of a checkbox leads to fewer incidents and greater peace of mind.
Establish Clear Safety Protocols
Setting comprehensive safety protocols provides a solid framework for avoiding accidents. Written policies should outline procedures tailored to specific workplace environments and potential hazards. These protocols must cover basic practices such as proper lifting techniques, use of personal protective equipment, emergency response actions, and hazard reporting processes. When employees understand expectations clearly, they are more likely to follow guidelines consistently. Regularly reviewing and updating these protocols ensures they remain relevant as conditions change or new risks emerge. Safety procedures that are visible, accessible, and reinforced by leadership create a culture where prevention becomes second nature.
Train Employees Thoroughly and Regularly
Employee training goes beyond initial orientation; it must be an ongoing effort that adapts to evolving challenges. Well-designed training programs focus on practical skills and knowledge employees need to navigate their roles safely. Hands-on demonstrations, interactive sessions, and real-world scenarios help cement learning far better than passive instruction. Training should emphasize recognizing hazards, proper equipment handling, and the importance of reporting unsafe conditions without fear of reprisal. Frequent refresher courses reinforce safe habits and keep everyone alert to subtle changes that may affect workplace safety. Empowering employees through education fosters vigilance and shared responsibility.
Conduct Routine Equipment Checks
Maintaining tools and machinery in excellent condition is crucial to preventing injuries. Equipment failure often leads to accidents, so systematic inspections and maintenance schedules reduce this risk considerably. Inspections should follow manufacturer recommendations and cover both visible wear and hidden mechanical issues. Documenting these checks establishes accountability and provides a record that safety standards are upheld. When equipment operates smoothly, employees can focus on their tasks without distraction or hazard. Integrating technology such as sensors or monitoring systems can also enhance preventive maintenance efforts by detecting problems early.
Promote Open Communication and Reporting
Encouraging employees to speak up about hazards and near misses is a cornerstone of injury prevention. An open communication culture invites honest feedback without fear of blame, which helps identify risks before they cause harm. Establishing clear channels for reporting concerns and ensuring timely responses demonstrates that safety is taken seriously at every level. Managers and supervisors who actively listen and act on reports build trust and reinforce that every voice matters. Regular safety meetings or briefings can also serve as platforms for sharing observations and updates. Transparent dialogue strengthens collective awareness and accelerates problem-solving.
Design Workspaces With Safety in Mind
Physical layout and ergonomics play a significant role in preventing workplace injuries. Thoughtful design minimizes strain, reduces trip hazards, and streamlines movement. Adjustable furniture, sufficient lighting, clearly marked pathways, and organized storage all contribute to a safer environment. Incorporating ergonomic principles tailored to job tasks helps avoid repetitive stress injuries and discomfort. Attention to detail in workspace design also includes ensuring emergency exits are accessible and that safety equipment is prominently placed. A well-designed environment invites careful habits and supports overall well-being.
Preventing injuries at work requires deliberate action and a mindset focused on foresight rather than reaction. Clear protocols set the stage, while comprehensive training equips employees with essential skills. Routine equipment checks ensure tools perform safely, and open communication channels uncover hidden dangers early. Thoughtful workspace design ties these elements together, reducing risks and promoting health. When safety becomes woven into every facet of the workplace, employees benefit from greater security and employers gain lasting operational strength. The effort invested in prevention delivers dividends in both human and business terms.
MORE ON THE FLASH LIST
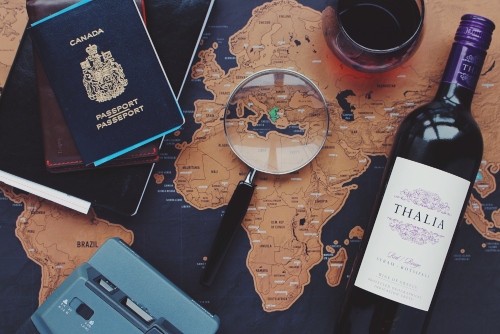